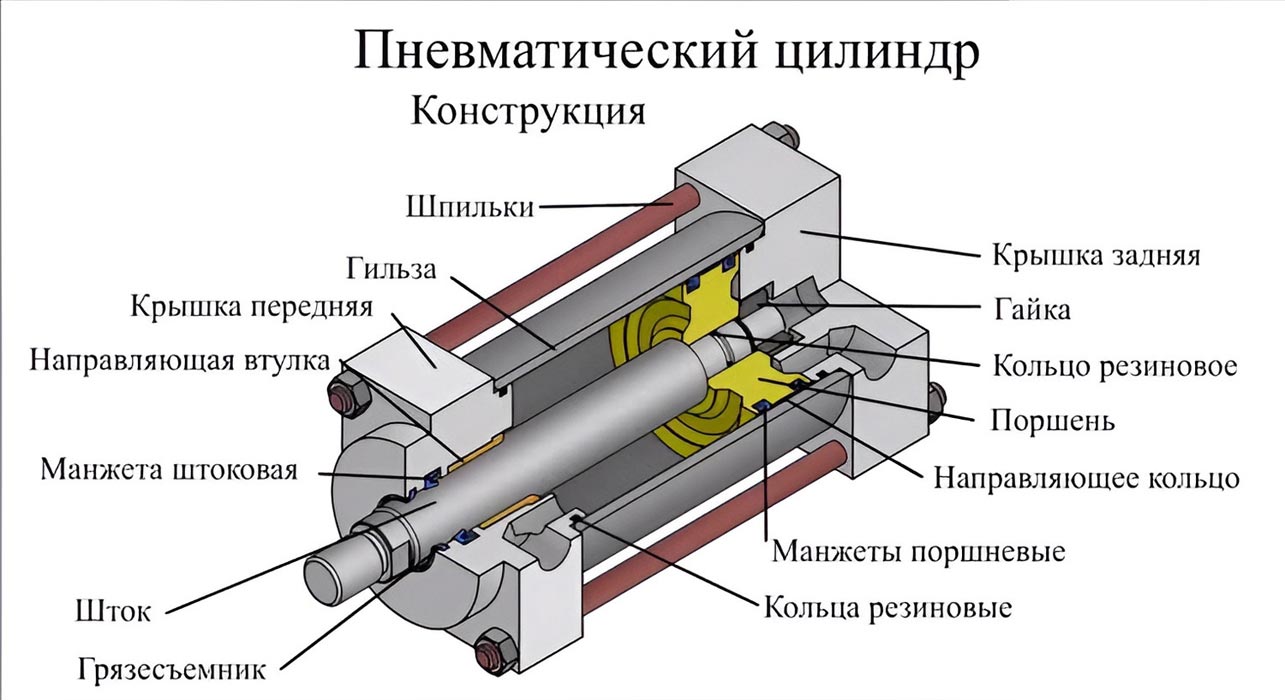
Пневмоцилиндр – это приспособления, предназначенные для линейного перемещения рабочего органа станков и других механизмов. Они играют важную роль в промышленности, облегчая выполнение различных операций и упрощая работу с механизмами.
Основным элементом пневматического цилиндра является полая гильза, внутри которой размещен шток. При помощи сжатого воздуха, шток внутри гильзы осуществляет движение, создавая силу, способную втягивать или толкать механизмы.
Преимущества использования пневматических цилиндров в механизмах заключаются в их высокой скорости работы, простоте управления и надежности. Они могут быть легко интегрированы в различные типы механизмов, обеспечивая эффективное и точное движение.
Пневматические цилиндры широко используются в автомобильной, пищевой, фармацевтической и других отраслях промышленности. Они являются неотъемлемой частью автоматизированных систем производства, обеспечивая высокую производительность и повышенную безопасность.
В заключение, пневматические цилиндры играют важную роль в промышленных процессах, обеспечивая линейное перемещение рабочего органа механизмов. Их простота управления, высокая надежность и эффективность делают их неотъемлемой составляющей современной промышленности.
Пневмоцилиндр - это незаменимый труженик в технологичном мире он облегчает как производство, так и жизнь людей давайте узнаем, как его делают и где применяют. Роботы на современных заводах помогают человеку выполнять тяжелую работу экономя время, именно пневмоцилиндр дает им выносливость до нескольких тонн, в общественном транспорте он плавно и бесшумно открывает двери, а потом плотно их закрывает, чтобы защитить от ветра и осадков.
Для начала инженер-проектировщик делает чертеж цилиндра просчитывает все детали и заносит данные в компьютер, затем он создает 3d модель, благодаря которой можно рассмотреть все части пневмоцилиндра теперь деталь можно собирать. Подготовленное сырье лежит на стеллажах, и ждет своего часа, штоки из легированной стали могут достигать 3 метров в длину а диаметр варьируется от 4 до 80 миллиметров, чтобы они стали сердцем будущего цилиндра их нарезают под нужную длину.
Готовый шток обрабатывают на шлифовальном станке убирая мелкие зазубрины, на конце металлического стержня необходимо нанести резьбу. Высокоточные станки выдавливают ее со скоростью от 6000 до 12 тысяч оборотов в минуту, такая технология экономит материал в отличие от накатки предполагающий срезания излишков металл один полный цикл занимает не более 2 минут, затем штоку придают зеркальную поверхность на полировальном станке, это улучшает его эксплуатационные характеристики - масляная смесь облегчает, и ускоряет процесс. Готовый стержень кладут на поддон, где стекут излишки масла эти трубы из анодированного алюминия будут служить корпусом нашему цилиндру, заготовку помещают в гильзу резку и под защитной крышкой специальная пила нарезает гильзу на нужные отрезки ее диаметр варьируется от 25 до 400 миллиметров таким образом станок производит сразу несколько деталей, в конце их достают из станка, обдувают от металлической стружки и отправляют на сборку.
Место встречи всех частей нашего цилиндра - стол мастера сборщика! Резиновый поршень надевают на металлический шток и накидывают шайбу резьбу на штоке обрабатывают фиксирующим герметиком, он не даст гайки раскрутиться и вывести цилиндр из строя, теперь поршень можно опустить в гильзу. Защитить внутренний механизм от грязи помогут 2 герметичные крышки в конце. Потом вручную проверяют плавность хода поршня всей конструкции, необходимо придать жесткость, с этим справятся стягивающие шпильки их пропускаю через специальное отверстие в крышках пневмоцилиндра и фиксирует гайками с двух сторон. Необходимо всего четыре таких шпильки чтобы деталь стала прочной.
Готовый цилиндр тестируют в два этапа на первом воздух под давлением подается внутрь корпуса погруженного одним концом в воду так проверяют герметичность крышек, на втором смотрят прямой и обратный ход поршня, деталь устанавливают на стенд, вводят необходимые параметры в компьютер в случае неполадок техника подаст сигнал. После тестов необходимо нанести гравировку, лазерный луч снимает верхний слой металла оставляя на корпусе все данные о нашем цилиндре.
Остался последний этап – упаковка. Сначала в цехе на каждый цилиндр надевают красную пластиковую сетку она служит для защиты внешних поверхностей цилиндра при транспортировке, готовые детали отправляются на тележке в упаковочный цех. Инновационная упаковочная бумага послужит мягким одеялом для цилиндра когда он поедет к покупателю, а фирменную коробку запечатывают и взвешивают на промышленных весах печатают стикер со штрих-кодом он содержит всю информацию о продукте теперь деталь можно отправлять.
Пневмоцилиндры используются во всех сферах нашей жизни от тяжелой промышленности до народного хозяйства. Они получают все большее распространение Пневоцилиндры camozzi - надежные и не требуют дорогих запчастей и сложного обслуживания, поршню внутри цилиндра предстоит пройти 16000 километров это гарантийный срок службы.
Эксклюзивные разработки компании camozzi для российского рынка, пневмоцилиндр от компании camozzi будет обеспечивать легкую и бесперебойную работу!